The 5 Keys to Insitu Project Success
- Specification
This does not need to be a formal detailed document, but needs to be better than “repair our pump”. Your supplier is not an expert on your equipment, they are machining experts and although they can often advise on possible repairs and what has been done on previous similar jobs do not expect your machining company to tell you what you need.
The specification should include;
Current condition, material spec, quantities, key dimensions, dimensional and geometrical tolerances, permitted material removal
It is also important to understand what will be permitted as part of the repair process – the insitu machine will need to be rigidly attached to the job and this may require tack welding on a service plate, drilling and tapping new holes, or utilising existing features. Parts of the plant may need to be removed to allow access.
- Accurate Information
Provide as much accurate information as possible, including drawings and photographs. Your machining company can advise the details required so please respond accurately to requests for information.
If you state 2”UNC threads, but they turn out to be 2” BSF, this small detail will mean preparation of the incorrect tooling, resulting in downtime as new tooling is sent – remember the insitu machining company cannot bring the whole machine shop to the job
If possible supply the following;
Dimensioned Drawings – if not available a sketch or marked up photo with key dimensions
Photos of the repair area and surrounding area – preferably with a tape rule in the photo to provide scale
Distances and clearance from any obstructions surrounding the area
The extent that the equipment or surrounding equipment be stripped back and removed – improving access and space by removing parts can have a dramatic impact on the machining duration
Condition of the material – what is the material specification? Has the material been heat treated, torched, hardened, exposed to high pressures and/or high temperatures or otherwise had its material properties changed?
What is the working environment – is it workshop conditions or outdoors, are there any specific hazards or training require e.g. confined space, rope access, working at height.
When the work is required? Almost all repairs are required ASAP – however ASAP to some is “we need you on site yesterday” – where the repair is holding up productions, to others it is desirable to have completed sooner rather than later but the project is not on critical path.
- Onsite Support
The insitu team are heavily reliant on services provided by you. Before the start of the job a detailed work pack should be presented by the machining supplier to the customer detailing the method statement and also their requirements which may include;
Power supplies – ensure that you have read and understood what is needed in the requirements section of our proposal. Ensure that the power is a dedicated supply and that others working in the area have been informed of this. Having the power pulled by somebody else is common and not only leads to down time but can be potentially dangerous e.g. using a magbase drill in an overhead position.
Mechanical Handling – despite being ‘portable’ much of the insitu machining equipment cannot be safely manhandled. Normally the equipment will need to fork-lifted out of our Vans, transported to the work area, and then lifted into position using a crane.
Scaffolding – Most jobs require some form of access platform of scaffolding. Often this requires slight modification once on site. A good rule of thumb is to have the platform at a height such that the work piece is between waist and chest height.
Welding – a fixture may need to be tack welded to the job, or weld build up prior to machining. Ensure that there is welding resource available when required.
It is also important to introduce the machinists to the “decision maker” and ensure that they are contactable / available when required. Depending on the project there may be a number of steps that require sign off or a decision to be made – e.g. acceptance of machine set up, what to do if component is not going to clean up before maximum material removal, discovery of additional repairs required when a crack is revealed
- Offsite and Onsite Preparation
For all but the most basic of pipe cutting or flange facing repairs there is no one size fits all insitu machine. The majority of insitu projects need some form of customisation, tooling to be ordered and some detailed planning.
Provide your insitu machining supplier with as much preparation time as possible. Avoid spending the week attempting the repair and then calling your insitu machining supplier on the Friday in a panic when the repair needs to be compled before the beginning of the following week!
The more preparation that can be carried out in the machine shop then the less time that will be spent on site carrying out the repair.
Remember that the first insitu machining company to arrive at site will not necessarily be the first to complete the job.
Ensure that the plant or equipment has been stripped, cleaned and de-greased, and that any openings have been plugged to prevent the egress of machining swarf propagating into other parts of your plant.
Make the environment as much like a machine shop environment as possible with good lighting (suitable to read the scale on a micrometre), suitable working platforms and dedicated services close to the job. If applicable ensure there is adequate weather protection for our machinists and equipment.
It is important that insitu machinists have full and sole working access to the work area – it is not acceptable to have others working overhead that could cause significant hazards such as injury from falling/dropped objects.
- Pricing
For most insitu repairs the cost of the repair will be an important measure of the success of the project. Ensure that the machining company is quoting against your specification. Take time to check quotations are like for like – don’t be caught out by selecting the cheapest option only to find out that they have not quoted for the full scope.
Do not fixate on the hourly rate – some machining companies will have a more expensive hourly rate but will complete the job in a shorter timescale resulting in a lower invoice value. A higher hourly rate will generally mean more pre-engineering and offsite engineering support.
Even in fixed price contracts, failure to supply the insitu company with the required services in a timely manner can result in waiting time costs and anything not quoted in the specification will be subject to extra work costs. Both of these additional costs are completely in the hands of the customer. Complying with the steps outlined above will keep additional costs to an absolute minimum
As part of the cost of the project remember to factor in the cost of lost operation for each additional day taken on site by the machining company to complete the repair – in some circumstances this can completely outweigh the machining cost where loss in production can result in significant loss of earnings.
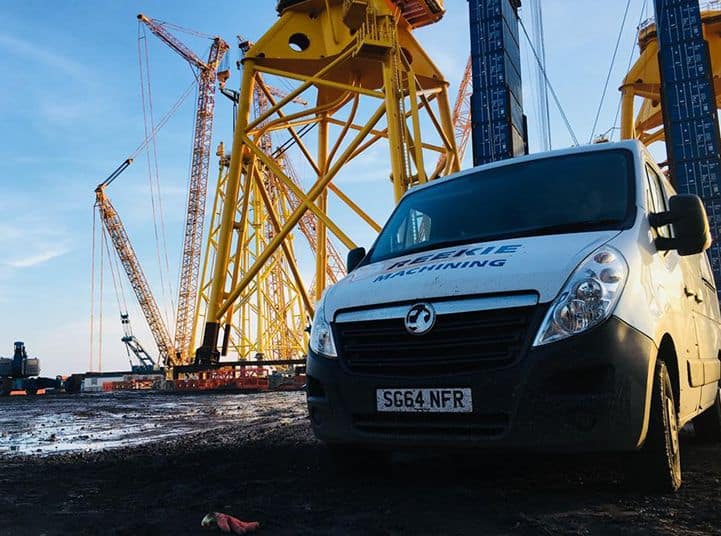
Insitu Project Details Form
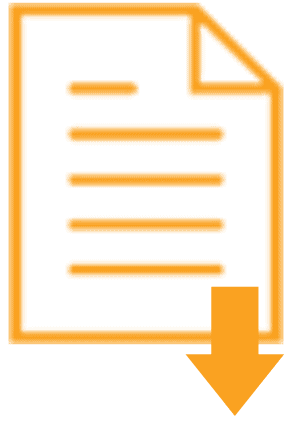